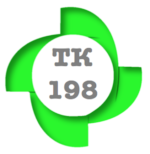
According to the order of UkrNDNC №97 of March 23, 2021, NBTR LLC became a member of the newly created Technical Committee for Standardization "Solid Recovered Fuel and Biofuels" - TC198


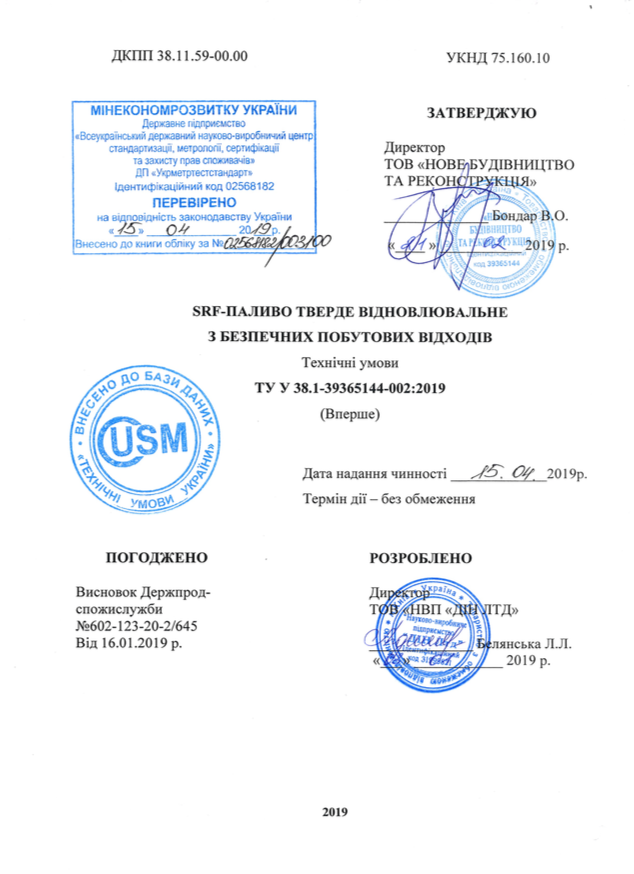

SRF-fuel
TU U 38.1-39365144-002: 2019,
Statement of the State Consumer Service, No. 602-123-20-2 / 645 dated 16.01.2019
(These specifications are the design and property of NBTR LLC)
RDF-fuel
TU U 38.1-39365144-001: 2018,
Conclusion of the State Consumer Service, №602-123-20-2 / 44642 dated 29.10.2018
(These specifications are the design and property of NBTR LLC)
FUEL FROM MUNICIPAL SOLID WASTE
RDF production line includes:
- Magnetic separators;
- Non-magnetic detectors;
- Primary crushers to the fraction of 100-400 mm. in size;
- Secondary crushers to the fraction of 3-30 mm. in size;
- Vibroscreens;
- Dryers wyth cyclone-filters;
When the secondary raw material is fully separated in sorting cabins, magnetic separators, non-magnetic detectors, the residual of MSW is transported to primary and secondary crushers. This residual includes:
- Wood and its derivatives;
- Leather, rubber articles;
- Multilayer package;
- Plastics;
and unseparated residual (the residual that can not be used as a secondary raw material) :
- Paper, cardboard and other paper waste;
- Textile;
- Plastics;
The quantitive index of such residuals variates around 35% from total amount of MSW. In case the plant is fully orientated to energy production, all the combustible raw material (including secondary raw material) is transported for RDF production. In this case, the quantitive index of produced RDF may raise to 50% from total amount of MSW. Also, in this case, appears an opportunity for RDF composition manual regulation (artificially forced enrichment) to achieve its homogeneity and maximum calorific value.
An average calorific value of RDF is accepted between 4200-5200 kcal/kg6 which corresponds to the lowest combustion heat 16-20 МДж/кг. If the artificially forced enrichment system is used, a high index of RDF homogeneity and caloricity is achieved. Herewith, the average combustion heat is taken at the level of 20 MJ/kg +/-2 МJ in all batches.
Indicators of the individual possible RDF components are shown in the table
№ | Component | Qphi |
МДж/кг | ||
1 | Bitumen | 41,9 |
2 | Paper | 13,4 |
3 | Textile | 16,2 |
4 | Wood | 14,7 |
5 | Chip-board | 16,8 |
6 | Cardboard | 13,9 |
7 | Linoleum, PVC base | 20,3 |
8 | Linoleum, PVC base | 39,8 |
9 | Transformer oil | 43,1 |
10 | Industrial oil | 42,3 |
11 | Motor oil | 41,8 |
12 | Plastic | 33,6 |
13 | PVC | 17,3 |
14 | Foamed polyurethane | 24,3 |
15 | Polyethylene | 47,1 |
16 | Resin | 33,5 |
17 | Polymeric petroleum resin | 32,1 |
18 | Polymeric synthetic fabric | 31, 1 |
19 | Plywood | 18,2 |
20 | Sawdust | 18,6 |
21 | Solid oil | 37,2 |
22 | Polymethylmethacrylate | 27,8 |
23 | Polyethylene terephthalate | 20,8 |
Characteristics of some polymeric components of MSW
Component | Composition, % | Lower heating value, Qн kcal/kg | ||||
с | н | о | n | cl | ||
Polyacrylamide | 57,8 | 6,0 | 18,6 | 17,6 | - | 5680 |
Polyvinyl acetate | 55,8 | 7,0 | 37,2 | - | - | 5270 |
Polyvinyl chloride | 38,7 | 4,9 | - | - | 56,4 | 4340 |
Isopropane rubber | 63,7 | 9,7 | 14,2 | 12,4 | - | 7180 |
Polypropylene | 85,7 | 14,3 | - | - | - | 11150 |
Polystyrene | 92,8 | 7,2 | - | - | - | 9280 |
Polyethylene | 85,7 | 14,3 | - | - | - | 10460 |
Polyethylene terephthalate | 62,5 | 4,2 | 33,3 | - | - | 5220 |
Polyamides | 38,9 | 5,9 | 8,6 | 7,6 | - | 7180 |
To obtain the optimal fuel composition a process chart of RDF composition is developed. Optical analyzers may be provided for installion after shredders and vibroscreens to fix the RDF composition and determine its caloric value in batches. The optical analyzer is installed after the secondary shredder and vibroscreens and it does a real-time analysis of the future RDF composition with data fixation for the following parameters:
- Calorific value in MJ;
- Humidity in %;
- Material composition;
- PVC content in %;
Data recorded by the optical analyzer is used as confirmation for RDF certificate.
After shredding and vibroscreening, the prepared raw RDF (pre-RDF) is moved to dryers with cyclone filters. When pre-RDF humidity reaches the level of 15-20% RDF it becomes a ready for combustion in boilers RDF.